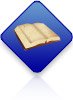
Technical Articles From Kester
Read technical articles about electronics manufacturing added by Kester
- SMTnet
- »
- Technical Library
- »
- Contributors
- »
- Articles from Kester
15 technical articles added by Kester
Company Information:
Reactivity Of No-Clean Flux Residues Trapped Under Bottom Terminated Components
Jul 20, 2017 | Bruno Tolla, Ph.D., Jennifer Allen, Kyle Loomis - Kester Corporation, Mike Bixenman, DBA - KYZEN Corporation
As electronic devices increase functionality in smaller form factors, there will be limitations, obstacles and challenges to overcome. Advances in component technology can create issues that may have time delayed effects. One such effect is device failure due to soldering residues trapped under bottom terminated components. If the residues trapped under the component termination are active and can be mobilized with moisture, there is the potential for ion mobilization causing current leakage....
How to Use the Right Flux for the Selective Soldering Application
May 17, 2017 | Bruno Tolla Ph.D, Denis Jean, Xiang Wei Ph.D
The selective soldering application requires a combination of performance attributes that traditional liquid fluxes designed for wave soldering applications cannot fulfill. First, the flux deposition on the board needs to be carefully controlled. Proper fine tuning of the flux physicochemical characteristics combined with a process optimization are mandatory to strike the right balance between solderability and reliability. However, localization of the flux residue through the drop jet process is not enough to guarantee the expected performance level. The flux needs to be designed to minimize the impact of unavoidable spreading and splashing events.
From this perspective a fundamental understanding of the relationships between formulation and reliability is critical. In this application, thermal history of the flux residues (from room temperature to solder liquidus) is a key performance driver. Finally, it is necessary to conduct statistically designed experiments on industrial selective soldering machines in order to map the relationships between flux characteristics and selective process friendliness....
Partially-Activated Flux Residue Impacts on Electronic Assembly Reliabilities
Dec 29, 2016 | Yanrong Shi, Ph.D., Kyle Loomis, Jennifer Allen, Bruno Tolla, Ph.D.
The reliabilities of the flux residue of electronic assemblies and semiconductor packages are attracting more and more attention with the adoption of no-clean fluxes by majority of the industry. In recent years, the concern of "partially activated" flux residue and their influence on reliability have been significantly raised due to the miniaturization along with high density design trend, selective soldering process adoption, and the expanded use of pallets in wave soldering process. When flux residue becomes trapped under low stand-off devices, pallets or unsoldered areas (e.g. selective process), it may contain unevaporated solvent, "live" activators and metal complex intermediates with different chemical composition and concentration levels depending on the thermal profiles. These partially-activated residues can directly impact the corrosion, surface insulation and electrochemical migration of the final assembly.
In this study, a few application tests were developed internally to understand this issue. Two traditional liquid flux and two newly developed fluxes were selected to build up the basic models. The preliminary results also provide a scientific approach to design highly reliable products with the goal to minimize the reliability risk for the complex PCB designs and assembly processes.
This paper was originally published by SMTA in the Proceedings of SMTA International
...Lead-free SMT Soldering Defects How to Prevent Them
Oct 23, 2012 | Peter Biocca, Senior Development Engineer
Tin-Silver-Copper alloys are the primary choice for lead-free SMT assembly. Although there are other options available such as alloys containing bismuth or indium and other elements, tin-silver-copper solders, also known as SAC alloys are by far the most popular. They are used by approximately 65% of users, as last surveyed by Soldertec in 2003....
SnCu Based Alloy Design for Lower Copper Dissolution and Better Process Control
Feb 13, 2009 | Peter Biocca, Senior Engineer, Technical Manager; Kester ITW,
To meet the market demand for a best-in-class, low-cost leadfree alloy for wave, selective and dip soldering...
Creating Solder Joint Reliability with SnCu Based Solders Some Practical Experiences
Jan 15, 2009 | Peter Biocca, Senior Market Development Engineer, Kester.
Tin-silver-copper has received much publicity in recent years as the lead-free solder of choice. SAC305 was endorsed by the IPC Solder Value Product Council in the United States as the preferred option for SMT assembly; most assemblers have transitioned to this alloy for their solder paste requirements. The SAC305 alloy due to its 3.0% content of silver is expensive when compared to traditional 63/37 for this reason many wave assemblers are opting for less costly options such as tin-copper based solders for their wave, selective and dip tinning operations....
Lead-Free Reliability - Building It Right The First Time
Jul 01, 2008 | Peter Biocca
As lead-free and RoHS compliancy fast approaches, it is more important than ever to build it right the first time. Lead-free assembly and RoHS will bring about numerous changes and the number of variables with which to contend is increasing, creating increased risk of defects and reduced product reliability. However, understanding what the variables are and their impact on the assembly can great increase product reliability....
Developing a Reliable Lead-free SMT Process
Jan 03, 2008 | Peter Biocca, Senior Development Engineer, Kester.
Lead-free SMT can be achieved reliably if several process requirements are implemented carefully. Some of the variables to account for are listed below. The most common alloys used in lead-free SMT are tin-silver-copper alloys; these alloys all have a meting range between 217- 220°C. These alloys all melt at higher temperatures than traditional leaded solders such as the 63/37which has a melting point of 183 °C....
Case Study on the Validation of SAC305 and SnCu Based Solders in SMT, Wave and Hand-soldering at the Contract Assembler Level
Nov 15, 2007 | Peter Biocca, Carlos Rivas
At the contractor level once a product is required to be soldered with lead-free solders all the processes must be assessed as to insure the same quality a customer has been accustomed to with a Sn63Pb37 process is achieved. The reflow, wave soldering and hand assembly processes must all be optimized carefully to insure good joint formation as per the appropriate class of electronics with new solder alloys and often new fluxes....
Manufacturing Considerations When Implementing Voc-Free Flux Technology
May 07, 1999 | David Scheiner, Senior Technical Service Engineer Kester
In 1990 the United States Environmental Protection Agency Issued the Clean Air Act. The Clean Air Act and subsequent amendments are designed to limit the use of chemicals that contain volatile organic compounds (VOCs). The document goes into great detail setting limits for allowable VOC emissions for different industries....
SMT Process Recommendations Defect Minimization Methods for a No-Clean SMT Process
May 07, 1999 | Kurt Rajewski
Key competitive advantages can be obtained through the minimization of process defects and disruptions. In today's electronic manufacturing processes there are many variables to optimize. By gaining an understanding of what the defects are, and where they come from, is a key step in the process towards defect free/six sigma manufacturing. In the last decade, Surface Mount Technology processes have been slowly converting towards the No-Clean philosophy. This new trend has spawned new processing issues which need to be addressed. This paper will investigate solutions to current problems in the processing of No-Clean SMT processes....
Soldering to Gold Over Nickel Surfaces
May 07, 1999 | Dennis Bernier
There are many things that can go wrong when soldering to gold plate over nickel surfaces. First of all, we know that gold and solder are not good friends, as any time solder comes into contact with gold, something seems to go wrong. Either the solder bonds to the gold and eventually pulls off as the tin and gold cross-migrate, leaving voids; or the solder completely removes the gold and is expected to bond to the metal which was under the gold....
Characterization of No Clean Solderpaste Residues: The Relationship to In-Circuit Testing
May 07, 1999 | Merlin Kister, Kester Solder
Many manufacturers have now completed the conversion to no clean solder paste. Many factors governed this initial conversion, among those being cosmetics, solder ability, and process ability. In circuit testing or probing through no clean solder paste residues has topically not been a major factor in the conversion decision for several reasons. Due to board design, solder paste was only used on one side of the board and not subjected to testing......
The Nature of White Residue on Printed Circuit Assemblies
May 07, 1999 | Dennis F. Bernier, Vice President, Research & Development, Kester Solder
White residue remaining after cleaning circuit board assemblies can be caused by a variety of chemicals and reactions. Rosin and water-soluble fluxes, circuit board resins and epoxies, component materials and other contamination all contribute to this complex chemistry. This paper discusses many of the sources of the residues that seem to be an ever-increasing occurrence....
The Effect Of Metallic Impurities On The Wetting Properties Of Solder
May 07, 1999 | Dennis Bernier, Kester Solder Company
This paper is a report of a study made to determine the maximum allowable impurities in solder used for wave soldering applications. This report concludes with a list of impurities compiled from actual analyses of solder which caused production problems. A list of recommended maximum allowable impurities will assist in establishing reliable quality controls on the purity level of the solder in a wave soldering machine....